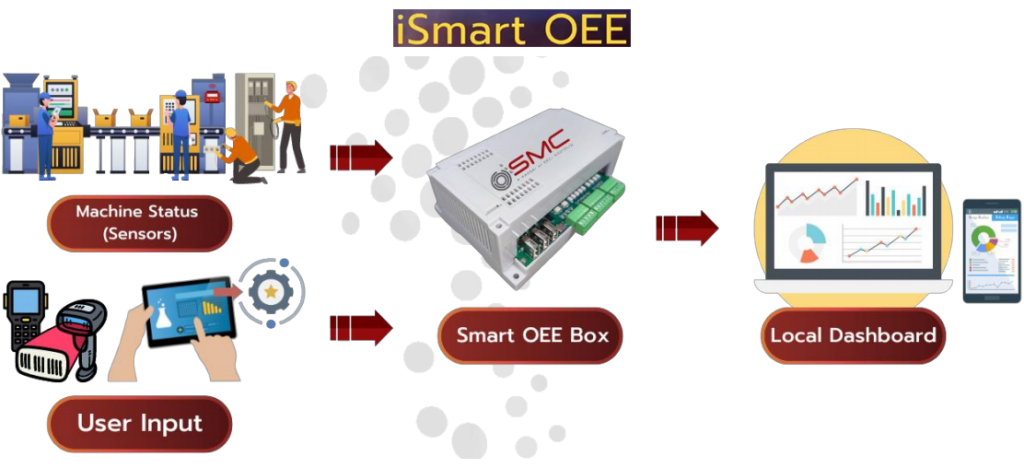
Key Benefit
Improved Production Efficiency
Optimizes machine utilization for maximum output
Enhanced Decision-Making
Uses data analytics to detect inefficiencies and trends
Reduced Production Costs
Reduces energy consumption and raw material waste
Increased Equipment Lifespan
Reduces unplanned breakdowns that shorten equipment lifespan
Higher Product Quality
Identifies and eliminates defects in real time
Competitive Advantage
Enables lean manufacturing and continuous improvement
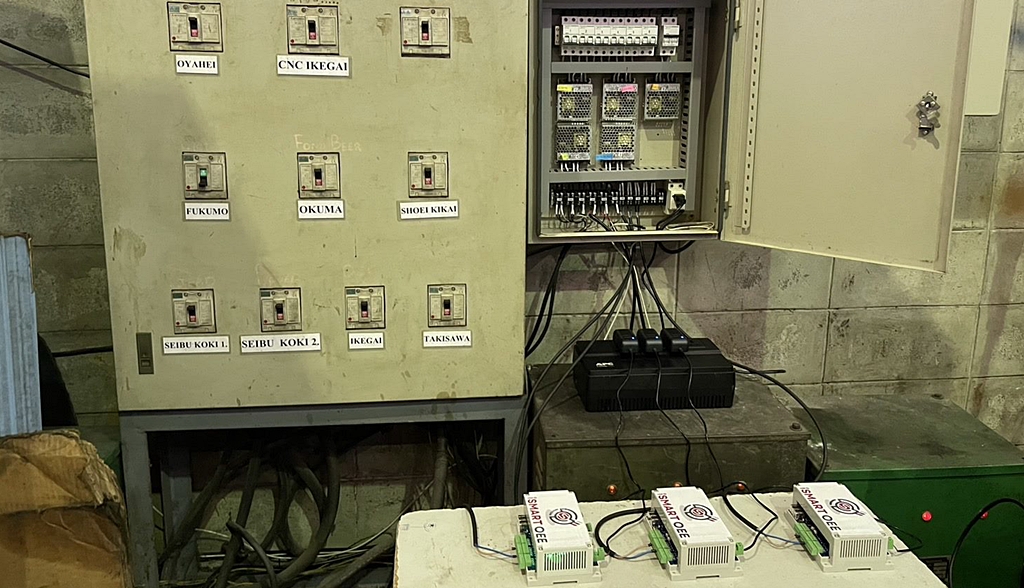
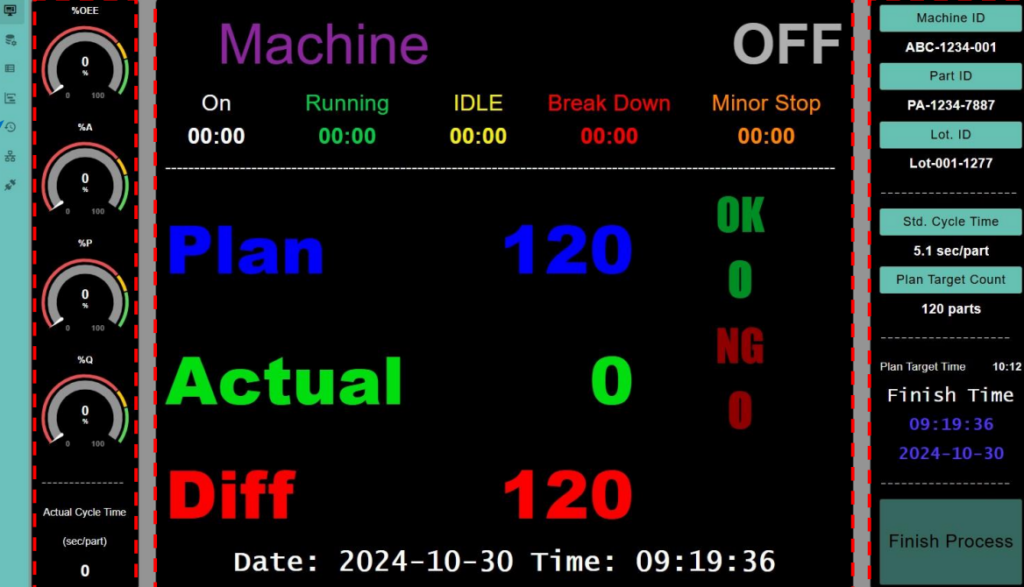
System Overview
Real-time automatic Overall Equipment Effectiveness (OEE) measurement system communicates with industrial protocols Modbus RTU, Modbus TCP, MQTT and RESTful API, reducing data recording, increasing speed of inspection and alerting of abnormalities in the production line.
The Smart OEE will check the working status of the machine, the number of products produced (FG) and damaged products (NG) by using an additional external sensor installed and then process the measured values into %A %P %Q and OEE values, including displaying the working status of the machine and the product production status at the machine front with a Local Dashboard and sending all data to the Server for display at the center.
Highlights/Benefits
- Provides information on standard (OK) and non-standard (NG) products, which are necessary for analyzing the production process, reducing time and errors in data recording
- Able to create a Local Dashboard to show the operating status of the machine, as appropriate for each factory
- Helps identify and analyze problems that affect the efficiency of the machine, such as a machine breakdown, in order to improve and develop a production plan to increase efficiency